Article No. 300425
Two-component multi-functional building waterproofing
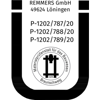
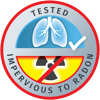
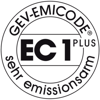
Product specifications
On delivery
(5 °C / 90% relative humidity) Approx. 24 h for a 4 mm layer
The stated values represent typical product characteristics and are not to be construed as binding product specifications.
Field of application
- Concrete basements, especially water-impermeable concrete basements
- Mineral substrates
- Exterior waterproofing in strip form for construction joints on concrete components with high resistance to pressing water penetration (water impact class W2.1-E)
- Waterproofing of new buildings according to DIN 18533 for water impact classes W1-E, W2.1-E, W3-E and W4-E
- Large-area and strip waterproofing according to the DAfStB WU Guideline
- Subsequent waterproofing of existing buildings according to WTA
- Bonding layer on old bitumen coatings
- Can be used for bonding and coating glass foam insulation boards
Properties
- Stable
- Can be applied to non-absorbent and weakly absorbent substrates without a primer
- Optimised for filling, minimal dripping loss
- Fast drying and crosslinking: 24 hours at 5°C and 90% relative humidity
- Radon-tight (verified through testing)
- Very low emissions (GEV-EMICODE EC 1Plus)
- Solvent-free
- Bitumen-free
- Water pressure tight
- High compressive strength
- Highly flexible, elastic and crack-bridging
- Surface has early resistance to rain after approx. 1.5 hrs
-
Preparation
-
Substrate requirements
The substrate must be clean, dry, flat and capable of bearing a load, and free of dust, oil, grease and release agents.
Roughen non-mineral and pore-free substrates.
Absorbent mineral substrates, not self-compacting concrete (SCC), may be slightly damp.
-
Preparations
Remove projecting seams and mortar remains.
Break off or chamfer corners and edges.
Produce the sealing cove with a suitable mortar.
Use a suitable mortar to seal construction joints in concrete basements.
Use a suitable mineral mortar or MB TX 2K mixed with suitable quartz sand (1:1 to 1:3 by mass) to close up cavities of more than 5 mm.
Large-pored substrates can be sealed beforehand with a scratch coat of MB TX 2K mixed with sand (Remmers Quartz Sand F 36).
Roughen the surface of plastic pipes; clean and, if necessary, sand metal pipes.
If necessary, provide damp proofing.
Prime absorbent mineral substrates with Kiesol MB.
Apply a scratch coat of the product as a contact layer and to prevent bubbles (approx. 500 g MB 2K TX/m²).
-
-
Preparation
-
Combination container
Stir the liquid component with a suitable mixing tool.
Loosen the powder component and add it in full to the liquid component.
Mix for approx. 1 minute before suspending the mixing process to allow the air that has been stirred in to escape.
Remove the powder adhering to the side.
Mix again for approx. 2 minutes.
Keep the mixing tool near the bottom of the bucket while mixing.
-
Application
-
Surface waterproofing
Apply the product in two layers on the previously prepared substrate.
Pipes passing through walls
W1-E: seal pipe penetrations by using the product to form a cove around them.
W2.1-E: use an adhesive flange or a suitable loose/fixed flange to integrate pipe penetrations into the waterproofing material.
Connection details/building element joints
Corners and connection joints should be bridged with Tape VF.
Apply the product, embed Tape VF over the entire surface, ensuring that there are no bubbles or creases.
Use Tape VF to connect to rising building elements (e.g. basement shafts).
Subsequent coatings
After 4 hours, work can be continued with adhesive mortar, filling
mortar or reinforcement mortar.
-
Application instructions
-
During application, the surface temperature of the substrate must be > 3 kelvin above the dew point temperature of the surrounding air.
In the case of liquid-applied waterproofing materials, direct sunlight and/or wind exposure can cause accelerated skin formation and accompanying blistering.
Do not use in direct sunlight.
Do not use on untreated aluminium.
The scratch layer does not as a rule count as a waterproofing layer.
The maximum total wet film thickness must not exceed 8 mm.
Moving the material (e.g. by stirring) in the mixing bucket can prevent premature skin formation.
Mortar that has already set cannot be made workable again by adding
water or fresh mortar.Protect the fresh waterproofing layer from rain, direct sunlight, frost and condensation water.
Once dry, protect from mechanical damage.
-
-
Working tools / cleaning
-
Mixing tool, scoop, layer thickness trowel
Clean tools with water while the material is still fresh.
Any material that has already begun to dry can only be removed mechanically.
-
Storage / shelf life
-
If stored unopened in its original container in a cool, dry place and protected against frost, the product will keep for at least 9 months.
-
Usage
-
Approx. 1.05 kg/m²/mm dry layer thickness
Approx. 4.2 kg/m² at 4 mm dry layer thickness -
Apply to a large enough trial area to determine the precise amount required.
-
Application examples
-
Water impact classes
(DIN 18533 / 18535)Dry layer thickness (mm) Wet layer thickness (mm) **** Application rate (kg/m²)
Yield 25 kg (m²) W1-E* Ground moisture and non-pressing water ≥ 3 approx. 3.1 approx. 3.1 approx. 8.1
W2.1-E**
Moderate impact of pressing water ≤ 3 m immersion depth ≥ 4*** approx. 4.2
approx. 4.2
approx. 6
W2.1-E**
Transition to components made from water-impermeable concrete
Moderate impact of pressing water ≤ 3 m immersion depth ≥ 4*** approx. 4.2 approx. 4.2 approx. 6 W3-E**
Non-pressing water on earth-covered slabs ≥ 3*** approx. 3.1 approx. 3.1
approx. 8.1
W4-E
Splashing water and ground moisture at the wall base, and capillary water in and under walls
≥ 2 approx. 2.1
approx. 2.1 approx. 12 W2-B Water loads in tanks with fill level ≤ 10 m ≥ 4 approx. 4.2 approx. 4.2 approx. 6
* Special agreement required for use on masonry** Special agreement required*** With reinforcement inlay (reinforcement fabric)Layer thickness allowance as per DIN 18533:du = scratch coat, application rate approx. 0.5 kg/m² (depending on the substrate)dv = not required with layer thickness trowel / application rate without layer thickness trowel approx. 0.4 kg/m² (dmin = 3 mm)
-
-
General information
-
The characteristic data of the product were calculated under laboratory conditions at 20°C and 65% relative humidity.
Certificates of suitability (abP) must be observed during planning and execution.
Special agreements and certificates of suitability can be downloaded online at www.remmers.com.
Always set up a trial area/trial areas first.
Peel tests are neither suitable nor authorised for assessing the suitability of the product for use.
-
-
Disposal instructions
-
Larger quantities of leftover product should be disposed of in the original containers in accordance with the applicable regulations. Completely empty, clean containers should be recycled. Do not dispose of together with household waste. Do not allow to enter the sewage system. Do not empty into drains.
-
-
Safety / regulations
-
For further information on the safety aspects of transporting, storing and handling the product and on disposal and environmental matters, please see the current Safety Data Sheet.
-