Article No. 298010
Stable hybrid waterproofing material for flat roofs and balconies
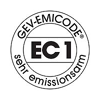
Product specifications
On delivery
BROOF (t1, t3 and t4) (EN 13501-5)
* This classification applies to the following applications: The product must be applied directly and with no air gap on flat building materials that correspond to class A1 or A2-s1, d0 pursuant to EN 13501-1 and must have a thickness of min. 6 mm and a bulk density of min. 1350 kg/m². Otherwise, the fire behaviour is to be rated as "Class E". Product characteristic data was determined under laboratory conditions (20 °C, 50% RH)
The stated values represent typical product characteristics and are not to be construed as binding product specifications.
Field of application
- Roof waterproofing in accordance with EAD 030350-00-0402 (formerly ETAG 005)
- Waterproofing of roofs, balconies, walkways according to DIN 18531
- Connections to lead-throughs and rising components
- New and old buildings
Properties
- Very low emissions (GEV-EMICODE EC 1)
- Surface waterproofing with reinforcement fabric
- Optimised for manual application on fine details and spray application
- Suitable for application with a trowel, brush, roller or sprayer
- Solvent-free
-
Preparation
-
Substrate requirements
The substrate must be level, stable, dry, clean, and free of dust, oil, grease and separating agents, see also the primer recommendation.
Absorbent mineral substrates may be slightly damp.
-
Preparations
If necessary, a contact layer of MB PUReactive TX can be applied to absorbent substrates at an application rate of approx. 500 g/m².
Fill depressions > 3 mm using a suitable filler.
-
-
Preparation
-
Combination container
Stir the liquid component with a suitable mixing tool.
Loosen the powder component and add it in full to the liquid component.
Mix for approx. 1 minute before suspending the mixing process to allow the air that has been stirred in to escape.
Remove the powder adhering to the side.
Mix again for approx. 2 minutes.
Keep the mixing tool near the bottom of the bucket while mixing.
-
Application
-
Processing time (+20 °C/50% RH):
90 minutesFollow-up work and coverings
Surface waterproofing + Detail waterproofing
Apply MB PUReactive TX to the prepared substrate using a suitable tool. Embed non-woven fabric of the MB PUReactive F-series correctly so that it is free of air pockets, and cover with the product (overall application rate min. 3.0 kg/m²).
Embed MB PUReactive F-series fleece overlapping at least 5 cm.
Recommendation: apply the product in the area of the overlaps between the layers.
-
Application instructions
-
The adhesion to the substrate must be tested on a case-by-case basis.
Always set up a trial area/trial areas first.
Direct sunlight and/or wind can cause accelerated skin formation on liquid-applied waterproofing materials.
Moving the material (e.g. by stirring) in the mixing bucket can prevent premature skin formation.
The contact layer (scratch coat) is not deemed to be a waterproofing layer.
The maximum total wet layer thickness must not exceed 4 mm.
The minimum dry layer thickness is 2.1 mm.
The dry layer thickness of the waterproofing layer must not fall below the minimum value at any point. To ensure that the minimum dry layer thickness is achieved, the product must be applied in a quantity that takes into account the layer thickness allowances (DIN 18531) so that processing tolerances, unevenness and roughness of the substrate are evened out. The quantity applied per square metre must be documented.
Protect fresh waterproofing from rain, frost and condensation.
Please contact Remmers Technical Service (phone +49 5432 83900) before applying with machine processing.
-
-
Working tools / cleaning
-
Mixing tool, flat brush, roller, smoothing trowel
Clean tools with water while the material is still fresh.
Any material that has already begun to dry can only be removed mechanically.
-
Storage / shelf life
-
If stored unopened in its original container in a cool, dry place and protected against frost, the product will keep for at least 9 months.
-
Usage
-
Approx. 1.5 kg/m²/mm dry layer thickness
Total application rate min. 3 kg/m²
Determine the exact requirement, taking into account roughness depth and application-specific allowances, on a sufficiently large test area.
Dry layer thickness: min. 2.1 mm
Wet layer thickness: min. 2.3 mm
Note the layer thickness allowance in accordance with DIN 18531-3:
DIN 18531 Part 3 stipulates a layer thickness allowance dz to ensure the minimum dry layer thickness dmin.
This takes into account both processing-related fluctuations dv and the additional amount needed for levelling the substrate du. If the substrate is levelled separately (e.g. by means of a scratch coat), du is not included in the calculation.
du = scratch coat or levelling allowance approx. 0.5 kg/m² (depending on the substrate)
dv = allowance for processing-related fluctuations approx. 0.4 kg/m²
-
General information
-
Seams, joints, connections and terminations as well as penetrations of existing waterproofing membranes must be designed to be resistant to backflow and sufficiently diffusion-tight. If required, a structural functional layer (vapour barrier) must be planned and implemented.
In the case of damp roof constructions, drying measures must be taken into account before applying the waterproofing and any existing structural defects must be inspected and rectified.
When waterproofing an inverted roof or a warm roof, suitable measures must be used to prevent the diffusion flow from inside to outside.
For the waterproofing of inverted and green roofs, please consult RTS Professional Planning (phone 05432 83434 + RTS-Fachplanung@remmers.de).
Current regulations and legal requirements must be taken into account and deviations from these must be agreed separately.
Certificates of suitability (EAD) must be observed during planning and execution.
Special agreements and certificates of suitability can be downloaded online at www.remmers.com.
-
-
Disposal instructions
-
Larger quantities of leftover product should be disposed of in the original containers in accordance with the applicable regulations. Completely empty, clean containers should be recycled. Do not dispose of together with household waste. Do not allow to enter the sewage system. Do not empty into drains.
-
-
Safety / regulations
-
For further information on the safety aspects of transporting, storing and handling the product and on disposal and environmental matters, please see the current Safety Data Sheet.
-