Chloride können in bewehrtem Beton zu erheblichen Korrosionsschäden führen. Daher ist der Beton besonders zu schützen. Dies gilt insbesondere für Verkehrsbauten, die sowohl den bewegten als auch den ruhenden Verkehr betreffen.
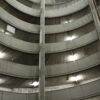
Concrete requires protection and needs to be repaired
Nothing is for ever
The production of compression resistant building components made of water-resistant mortars and stone blocks that harden in form work became established in the 1st century a.C and later became standard for late Roman-Imperial architecture. Today’s word ‘concrete from the Roman word ‘opus caementitium’ based on Vitruv has been used to erect fantastic and monumental construction works throughout Europe that can still be visited today even 2000 years later.
The concrete construction method was forgotten in the Middle ages and was rediscovered around 1700. Since then, concrete has become the building material of our time. Despite the high quality and resistance of concrete, damage can occur that makes repairs and additional protection necessary.
Damage to concrete buildings
Damage to reinforced concrete structures can be classified into damage to the concrete itself, concrete corrosion, and damage resulting from the reinforcement, steel corrosion.
Concrete corrosion:
Generally, outside influences can lead to the destruction of the concrete. Examples are:
• Frost attack with and without de-icing agents
• Chemical attack
• Abrasive load
The different types of concrete corrosion is classified depending on the ambient conditions (acc. to DIN EN 206-1 / DIN 1045-2) to which a concrete structure is exposed.
Steel corrosion:
In new concrete, the steel is protected from corrosion by the high level alkalinity of the pore water (pH ≥ 12.5). In this range of pH values, a microscopically thin oxide layer is created on the steel surface that practically suppresses the iron dissolution. If as a result of carbonation the pH value of the concrete drops to a value below 10 or the chloride content exceeds a critical limit value, the ‘natural’ corrosion proof is lost. If moisture and oxygen is present at the same time, the steel will corrode. As the corrosion products take up a larger volume than the output materials, the covering concrete often spalls.
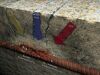
Repair systems
All damage requires individual repair solutions. In cooperation with the Remmers specialist planning department, correct repairs with professional systems are guaranteed.
Remmers is setting completely new standards in the concrete repair field. The Betofix assortment allows concrete repairs, from corrosion proof through to coating, in just one day. This not only saves time but also money. In addition, Betofix stands out thanks to its special properties and durability. A very important property of repair mortars for extremely polluted hydraulic structures is the chloride migration coefficient. Chlorides in reinforced concrete leads to substantial corrosive damage which is why a high penetration resistance should be the goal. Corresponding tests were developed originally for salt-water-polluted concrete structures. Its result can be transferred to all concrete structures that are heavily polluted with water containing de-icing agents.
This applies notably for traffic structure that affect both moving and also stationary traffic. Typical examples are car parks or underground car parks and here, notably, the columns and support bases that are frequently exposed without protection to the de-icing salts brought in by the vehicles. The use of Betofix R4 leads to a damage-free standing time that is more than four times as long than the best comparable product. Remmers Betofix R4 shows results as early as after 28 days, which is twice as good as the competition. The result further increases as the reaction time progresses.
A multiplicity of damage to concrete structures is created by cracks and hollow spaces that allow harmful substances to enter the structure. These harmful influences impair the function of the concrete and consequently considerably reduce the load bearing capacity of the construction work. The most common causes of cracks are shrinkage, a change to static conditions due to subsidence, inherent stress in the part, climate fluctuations (especially frost) and corrosion of the reinforcement. The concrete can be fully utilised and made serviceable again thanks to borehole injections or saturation of the faulty areas with suitable crack-filling substances. To be able to define the crack repair goals, accurate information is required about the moisture at the edges of the cracks, the change of the crack width and the course of the crack.
Preventing moisture penetrating building materials is one well-known way of protecting construction works that has been practised for many centuries. Even Vitruv described the use of natural oils to make mortar water repellent and therefore more resistant in his work ‘De Architectura Libri Decem’. Today, these functions are assumed by modern protective substances whose effectiveness and durability are ensured by high-quality materials and binding agents.
Coatings and impregnation serve as a protective layer with different functions. In addition to preventing the penetration of damaging substances into the concrete and the associated regulation of the moisture balance and increase of the electrical resistance, the physical resistance capability can also be improved. There is also the possibility of rigid or flexible crack-bridging and great creative versatility with tested surface protection systems from OS 1 to OS 11.