In der Lebensmittelindustrie treten häufig starke mechanische Belastungen neben extremen Temperaturspitzen durch heiße Flüssigkeiten auf. Viele dieser Flüssigkeiten enthalten aggressive Stoffe wie z.B. Milchsäure oder Essigsäure. Polyurethan-Beton hat sich seit Jahren als geeignetes Bodenbeschichtungssystem für unterschiedliche Lastfälle bewährt.
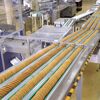
Floor requirements
Every industrial or commercial sector has different requirements with respect to floor coating. Remmers is the perfect surface protection system for many extreme requirements.
Temperature resistance: The first requirement for the stipulation of the Remmers System is the required temperature resistance. This not only defines the system composition, but also the layer thickness of the flooring.
Chemical resistance: Industrial floors are exposed to a variety of chemical substances every day. Concentrated chemicals varying from potassium hydroxide, acetic acid through to citric acid are used in the food industry. Whilst some substances hardly endanger, many substances corrode concrete floors and floor coating systems. Conventional synthetic resin coatings cannot withstand the constant exposure to aggressive media. Remmers Crete floors stand out thanks to their enormous resistance to a multiplicity of chemicals.
Resistance: Mechanical durability is an important selection criterion for the correct floor. To ensure that the floor functions in the long term, Remmers systems with high layer thicknesses and slip-resistant surfaces must be used in heavily frequented areas.
Food-safe: Remmers systems do not emit any constituents to food that are hazardous to human health.
Epoxy coating types
Remmers epoxy floor coverings are solvent-free and physiologically safe after curing. The serviceability for use as a jointless finish in the food industry has been tested and confirmed by external institutes. The systems stand out thanks to their high mechanical and good chemical resistance. Efficient systems can be created from a combination of special epoxy resins binding agents and matched filler substances that are suitable for various application areas. Thanks to these and many other properties, the products and systems have proven reliable for use as floor coatings in the food industry.
Sealings have a protective effect against slight to medium loads, and represents an economic solution with a layer thickness of up to 0.5 mm.
Properties
• Protects reliably (e.g. against weak acids)
• Follows the surface structures
• Slight mechanical durability
Application
• Production and storage areas
• Ancillary rooms
• Social rooms
Flow coats can compensate smaller areas of unevenness on the subsurface. The material is distributed evenly and flows on through which it creates a smooth surface. A layer of a thickness of up to 3.0 mm. Depending on the system, claw cuts according to the information in the technical code of practice may be necessary.
Properties
• Self-flowing
• Medium mechanical and chemical resistance
• Evens out smaller areas of roughness
Application
• Areas which require sure footing
• Areas with dynamic loads
The grano sprinkling finish comprises a flowable base coat into which the blinding materials are added in full (e.g. quartz sand or Hard Stuff). After setting, the unbound excess is removed and a topcoat is applied. The layer thicknesses may vary between 1.5 and 9.0 mm. Depending on the system, claw cuts according to the information in the technical code of practice may be necessary.
Properties
• High mechanical durability depending on the system
• Slip-resistant, safe surface that can be set individually
Application
• Permanently wet areas
• Metal working
• Food industry
The mortar coat has the lowest amount of binding agents and a finely matched filling material grading curve. The mortar mix is applied in an even layer thickness, and then compressed and smoothed. The minimum layer thickness is three times the respective largest grain of the filling materials used.
Properties
• Very high mechanical durability
• Compensates larger areas of unevenness
• Slip-resistant
• Can also be installed on gradients
Application
• Food industry
• Metal working
• Production areas
Coating types with PU concrete
Flexible and safe at the same time - Remmers Crete PU-concrete is the perfect combination of aqueous polyol emulsion and polyurethane binding agent made of polymer methyl-diisocyanate. This makes the floor extremely resistant to thermal, chemical and mechanical loads. Thanks to its components, the system can also be adapted to the various requirements of the food processing operations. The surface structure can be created to be smooth or structure by means of the blinding materials - ideal for the optimum anti-slip resistance of the floor.
Sealings have a protective effect against slight to medium loads, and represents an economic solution with a layer thickness of up to 0.5 mm; they follow the surface structure and can only compensate light roughness differences.
Properties
• Protects reliably (e.g. against weak acids)
• Follows the surface structures
Application
• Concrete floors subject to slight to medium loads
• Production and storage areas
The grano sprinkling finish comprises a flowable base coat into which the blinding materials are added in full (e.g. quartz sand or Hard Stuff). After setting, the unbound excess is removed and a topcoat is applied. The layer thicknesses may vary between 1.5 and 9.0 mm. Depending on the system, claw cuts according to the information in the technical code of practice may be necessary.
Properties
• High mechanical and, depending on the system, thermal durability
• Slip-resistant, safe surface that can be set individually
Application
• Permanently wet areas
• Metal working
• Food industry
Flow coats can compensate smaller areas of unevenness on the subsurface. The material is distributed evenly and flows on through which it creates a smooth surface. The layer of a thickness of up to 3.0 mm is applied. Depending on the system, claw cuts according to the information in the technical code of practice may be necessary.
Properties
• Self-flowing
• Pigmented
• Medium mechanical and chemical resistance
• Evens out smaller areas of roughness
Application
• Areas without sliding agents that require sure footing
• Areas with dynamic loads
The mortar coat has the lowest amount of binding agents and a finely matched filling material grading curve. The mortar mix is suitable for use with blades and then needs to be smoothed with a trowel. The layer is at least 4.0 mm thick. Depending on the system, claw cuts according to the information in the technical code of practice may be necessary.
Properties
• Very high mechanical durability
• Compensates larger areas of unevenness
• Slip-resistant
• Can also be installed on gradients
Application
• Areas which need to be slip-resistant
• Areas where no displacement factor is specified